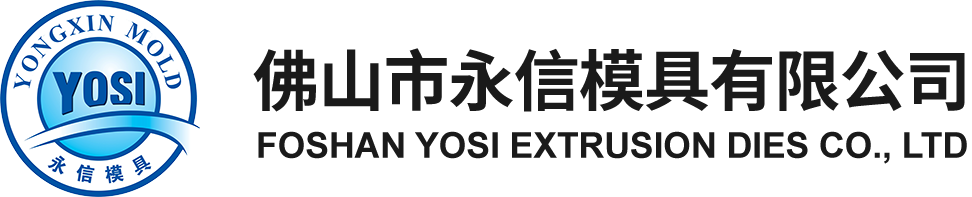
随着产品微米和纳米科学技术的发展进步,产品不断向微型化方向发展,特征尺寸为微米级的微电机系统的开发应用,微结构零件生产就面临着如何改善和优化生产的基本工艺条件,降低加工成本,实现零件的高速、高效、高精度和大批量生产等具体问题,其中,始于20世纪80年代的微量注射成型工艺,便开创了精密微细零件低成本、大批量生产的新途径,是世界先进制造技术重要的研究热点之一,慢慢的变成了生产这类塑件的主要技术。
微量注射成型技术的发展有赖于微量注塑机的发展,由于普通注塑机已不适应微量注射成型工艺的要求,进人20世纪90年代,欧洲、日本、美国和中国的一些公司与相关的科研机构合作,共同开发了很多类型的微量注塑机。
微量注塑机的基本功能通常包括塑化、计量和注射三部分。微量注塑机与普通注塑机的区别,大多数表现在塑化、注射单元机构和各部分的驱动方式上。当前微量注塑机的塑化与注射单元机构有螺杆式、柱塞式、螺杆-柱塞合式等;驱动方式主要有全液压式、全电动式和电动-液压复合式。
在模具方面,微型注塑对于加工设施的要求相对传统注塑要高很多。微型注塑在模具加工方面通常有两种趋势:
第一种是采用镜面火花机加工,为了确认和保证高精密度,最好要使用石墨电极进行电火花加工,因为石墨电极的损耗比普通的铜电极要小很多。
第二种很常用的加工方式是采用电铸模,采用电铸工艺能保证非常高的精度,但缺点是加工周期长,每一穴都要独立加工,还有在生产中如果有轻微损伤无法修复,只能重新更换损坏的穴位。
在模具方面,模温也是微型注塑的一个很重要的参数。面对高端需求的客户,目前很常用的做法是借用高光注塑领域的理念,导入快速加热与冷却系统。
理论上,高模温对于微型注塑很有帮助,比如可以有效的预防薄壁填充困难、缺料,但是过高的模具的温度又会带来新的问题,比如周期加长以及开模后收缩变形等。所以导入新的模具温控系统显得相当的重要,在注塑的过程中模具的温度可以提高(可以超过所用塑料的熔点),使得熔体能快速充满型腔,防止熔体在充填过程中温度降低过快而造成充填不全;而当脱模时,模具的温度又能迅速的降低,保持在比塑料热变形温度稍低的温度内,然后再开模顶出。
除此之外,由于微型注塑成型的是质量为毫克级的制品,如果采用普通浇注系统来注塑制品,即使是在作了最优化改进后,制品和浇注系统内的物料质量比仍为1:10。只有不到10%的物料被注塑成微型制品,产生大量浇注系统凝料,所以微型注塑应该采用热流道浇注系统。
材料选择方面,建议在开发前期就可选择一些粘度低、耐热性好的工程塑料。选择低粘度的材料是因为在充填过程中熔体的粘度低,整个浇注系统的阻力就相对小,填充速度较快,能保证熔体顺利充满型腔,熔体温度也不会有明显的降低,否则在制品上容易形成冷接缝,而且在充填过程中分子取向少,所得制品的性能比较均匀。
如果选择高粘度塑料,不仅填充较慢,而且补料时间较长,由于补料引起的剪切流动容易使链状分子沿剪切流动方向取向,在这样情况下冷却到软化点以下时取向状态被冻结,而这种在一定程度上的冻结取向容易造成制品的内应力,甚至引起制品的应力开裂或翘曲变形。
要求塑料的热稳定性高的理由则是由于物料长时间停留在热流道内或受螺杆剪切作用易引起热降解,尤其是对热敏性塑料,即使在很短的循环时间内,也会因为物料注射量小,在浇注系统内的停留时间相对较长,造成塑料相当程度的降解,因此热敏性塑料不适合微型注塑。
在注塑设备选用方面,由于微型注塑件尺寸大小为微米级别的制品,宜选用注射量为毫克级的注射机。
这类注射机的注射单元一般都会采用螺杆-柱塞组合式,由螺杆部分完成对物料的塑化,并由柱塞将熔体注人到型腔。螺杆柱塞式注塑机能结合螺杆的高精度与柱塞设备的高速度,能保证生产的全部过程的精度和填充速度。
此外,这种注射机通常由合模导向机构、注射系统、气动脱模机构、质量检验机构和自动包装系统组成。良好的质量检验系统可保证微型精密注塑制品的成品率,监控整一个完整的过程中的参数波动情况。
在微型功能件的注塑工艺上,我们应该考虑浇口的气痕与应力问题,通常需要采用多级注塑,确保材料能够处于稳流的状态填充。除此之外,还需要仔细考虑保压时间的大小,太小的保压压力会导致产品的收缩,但是过大的保压又会导致应力集中,以及尺寸变大等问题。
另外,材料在料管中停留的时间同样是需要严格监控的,材料在料管中停滞时间太长,会导致材料的降解影响产品的功能。建议在工艺参数管理上要进行标准参数管控,每个产品在量产前最好能够做工程控制验证,生产中所有的改动都要重新进行尺寸和功能的测试。
微型注塑作为注塑领域中的一个分支,正朝着高尺寸精度,高功能需求,高外观要求的方向发展,只有通过模具、设备、材料、工艺等各个流程的严控和技术逐步的提升才能满足巿场的发展。返回搜狐,查看更加多