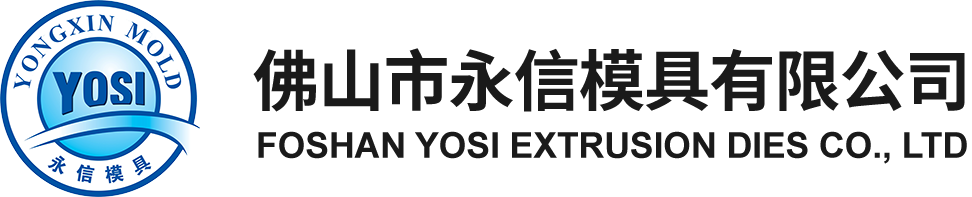
日常生活中,那些装化妆品、口服液、巧克力的塑料盒都是采用真空吸塑成型工艺,那么具体的工艺流程是怎样的?用到了哪一些材料、设备呢?下面一起来了解下。
真空吸塑成型工艺,是一种热成型加工方法。利用热塑性塑料片材,制造开口壳体制品的一种方法。将塑料片材裁成一定尺寸加热软化,借助片材两面的气压差或机械压力,使其变形后覆贴在特定的模具轮廓面上,经过冷却定型,并切边修整。真空吸塑成型这种成型方法是依靠真空力使片材拉伸变形。真空力容易实现、掌握与控制,因此简单真空成型是出现最早,也是目前应用最广的一种热成型方法。
PVC:最常用的吸塑材料,质软、韧性强、可塑性好,可做成透明和各种颜色,常用透明PVC包装电子、化装品、玩具礼品等产品。
PET(A-PET):质硬,韧性好、强度高、表面光亮、环保无毒,有透明和多种颜色的片材。缺点是PET高周波热合很难,价格也比PVC贵很多,此材料常被要求产品高档和环保的用户取代PVC。
PS:密度小(质轻)、环保无毒,可塑性非常好,韧性差易脆,不可做成通明材料,因此只能做成底托类吸塑,因其易裂,此类吸塑不宜回收。
PP:材质特别软,韧性好,环保无毒、耐高温,常被做成餐饮器具或其他耐高温产品的包装;但其可塑性差,加工难度大,表面光泽度差,而且加工时颜色会变浅。
PET-G:物理性质同A-PET差不多,但可以高周波热合,其价格比A-PET还贵80%
普通薄吸塑厚度为0.14~5.0mm―――主要是采用PVC、PP、PS(HIPS)、PET(包括APET和PETG)、PE、BOPS和可回收纸托等各种材质与效果的折边、对折、三折、圆筒、折盒、天地盒、高周波等非热成型吸塑制品,大范围的应用于食品、医药、电子、玩具、电脑、日用品、化妆品和机械五金等行业。
特殊厚吸塑厚度为0.14~8.0mm―――主要是采用PVC、PP、PS(HIPS)、PET(包括APET和PETG)、ABS、PC、PE和PMMA等各种材质与效果的注塑类型吸塑制品,基本的产品有冰箱内胆、广告灯箱、商品展示架、宠物笼底盘、背投电视后壳和各种机械面板等,可以替代注塑产品,具有模具费用低(只有注塑模具的1/20),生产周期短,模具开发时间短(一般只要3~5天)等特点。
之所以不就材料的种类来进行分类,主要是考虑到普通薄吸塑与特种厚吸塑所采用的材料有一些区别,但是PVC、PP、PS和PET却在这两类吸塑制品中都占有一席之地,堪称吸塑制品用材家族的“四大天王”!
PVC硬片韧性适中,不易燃烧,燃烧时会产生氯气,对环境能够造成一定影响,PVC易热合,可采用封口机和高频机封边,是生产透明吸塑制品的主要原料。
PS硬片密度低,韧性差,易燃烧,燃烧时会产生苯乙烯气体(属有害化学气体),所以一般用来生产各种工业用的吸塑托盘。
PET硬片韧性好,透明度高,易燃烧,燃烧时不产生有害化学气体,属于环保材料,但价格高,适宜做高档的吸塑制品,欧美国家的吸塑泡壳一般要求采用PET硬片,但其不易热合,给封装带来很大困难,未解决这一问题,人们在PET表面复合上一层PVC膜,取名为PETG硬片,但价格更高一些。
吸塑设备系统有多设备组成,包含夹紧设备、加热设备、真空设备、压缩空气设备、冷却设备、脱模设备、控制设备等。
吸塑模具也分多种,有石膏模、胶模、电木模、电解铜模、合金铝模、热合模具、高频模具、刀模、冲孔模等。
吸塑片材也分多种,有PET(聚对苯二甲酸乙二酯)、PVC(聚氯乙烯)、PS(聚苯乙烯)、PP(聚丙烯)等。其中PS密度低,韧性較差,易燃烧一般用来生产各种工业用的吸塑托盘。PVC硬片韧性适中,不易燃烧但对环境能够造成一定影响。PET韧性好,透明度高,易燃烧,燃烧时不产生有害化学气体,属于环保材料。
加热软化塑料薄片雏形、内部空气通过阳模的抽气孔被抽出,软化塑料薄片雏形在空气的压力下吸附在阳模表面成型,冷却固化后,进行修边处理。
真空无模成型的过程如图所示,将片材加热到所需温度后,置于夹持环上,用压环压紧,打开真空泵阀门抽真空,通过光电管控制真空阀调节真空度,直到片材达到所需的成型深度为止。由于自由真空成型法中制件不接触任何模具表面,制件表面光泽度高,不带任何瑕疵。
1、检查板材表面的清洁,将中密度板表面的木碎和纤维吹走,保持表面没有灰尘,过多的灰尘和纤维将会引起麻脸现象。
2、对于切割好的中密度板,其四边打磨时,应选用尽量细的砂纸打磨。这样在喷胶过程中,中密度板的四边不会因为纤维过于粗糙薪而导致吸胶不均,从而引起麻点现象。对于外观要求比较高的制成品,建议使用的砂纸细度为800目以上。
1.不同的PVC膜对高温有不同的反应,如有更改材料,应先评估操作条件后才大量生产。
2.尽可能使用增塑剂含量低的PVC膜,因为薄膜内的增塑剂在长时间储存及高温环境下,有可能游离出表面,进而影响粘接效果。
2.如果用户对制成品的耐热要求超过70℃或生产车间温度、湿度过高时,建议加固化剂使用,固化剂用量在3%一5%。
2.通常,平面的喷胶量为:55—85g/㎡,轮廓面的喷胶量为:75一125 g/㎡。
粘合剂干化后,进机台吸塑,称为干式吸塑。一般在室温25℃情况下,胶水干化时间为10—20分钟。30℃—40℃环境下,胶的干化时间为3—10分钟。建议用户在胶膜完全透明后,即可吸塑。干化时间过长,影响粘接效果。特别是对于加固化剂的粘合剂,应尽量缩短干化时间,喷胶干后一小时内必需完成吸塑,否则会影响效果。
粘合剂在湿的状态下,即进机台吸塑,称为湿式吸塑。湿式吸塑主要是针对用户设备无法达到粘合剂的最低活化温度或PVC膜耐温性能很差的情况下使用。由于粘合剂在吸塑过程中水份未完全挥发,因此,吸塑时间要比干式吸塑长。通常情况下,尽可能少用湿式复合,特别是加热时间短的吸塑操作,否则,成品有可能出现“滑胶”的现象。
1.最低活化温度系指在吸塑操作的流程中,吸塑胶活化产生粘结性能所需的最低温度,相应于胶膜层所能达到的温度,而非机台设定温度。通常情况下,吸塑温度越高,越有利于胶膜对PVC膜表面的浸润,对粘接效果有利。但用户往往会考虑PVC膜的耐热程度,而降低吸塑温度。
2.一般来说,粘合剂要求吸塑的最低活化温度应高于55℃(60℃更优),也就是说在吸塑过程中,胶层表面的温度必须高于55℃。温度过低,会影响粘接效果及制成品的耐热性能。
八、线.真空度取决于不同的吸塑设备、不同的PVC膜厂家、不同PVC膜的厚薄、吸塑温度、板材表面的轮廓度、板材摆放位置等,用户应通过你自己的真实的情况做相应的调整。
2.通常情况下,根据经验,对于0.16mm一0.20mm厚的PVC膜,在机台设定温度为110℃~140℃条件下,其线Mpa。
九、抽线.抽真空时间取决于:PVC膜的软硬度、吸塑温度、板材的轮廓度、真空度等,用户应通过你自己真实的情况做相应的调整。
2.通常情况下,根据经验,在确保吸塑温度达到粘合剂最低活化温度、PVC膜充分软化条件下,线MPa,抽线分钟。
1.对于有胶囊的吸塑设备及部分无胶囊的吸塑设备,在抽真空时,上成型仓会注入热空气形成高压,确保PVC膜贴紧中纤板,压力的大小取决于:吸塑温度、PVC膜厚薄、板材轮廓度、真空度等,用户应通过你自己真实的情况做相应的调整。
3.对于部分无胶囊的吸塑设备,在吸塑时只有抽真空,没有加压,为确保吸塑效果,其真空度应相应调高。
吸塑好的成品出机台即可搬运,如果要进行下一步的工序,最好等产品完全冷却,产品做性能测试,则在3天后进行。
脑洞变现实,储能混凝土它来了!可为太阳能供电的家庭提供超过27年的储能